Proces relokacji linii produkcyjnych - od demontażu do ponownego uruchomienia
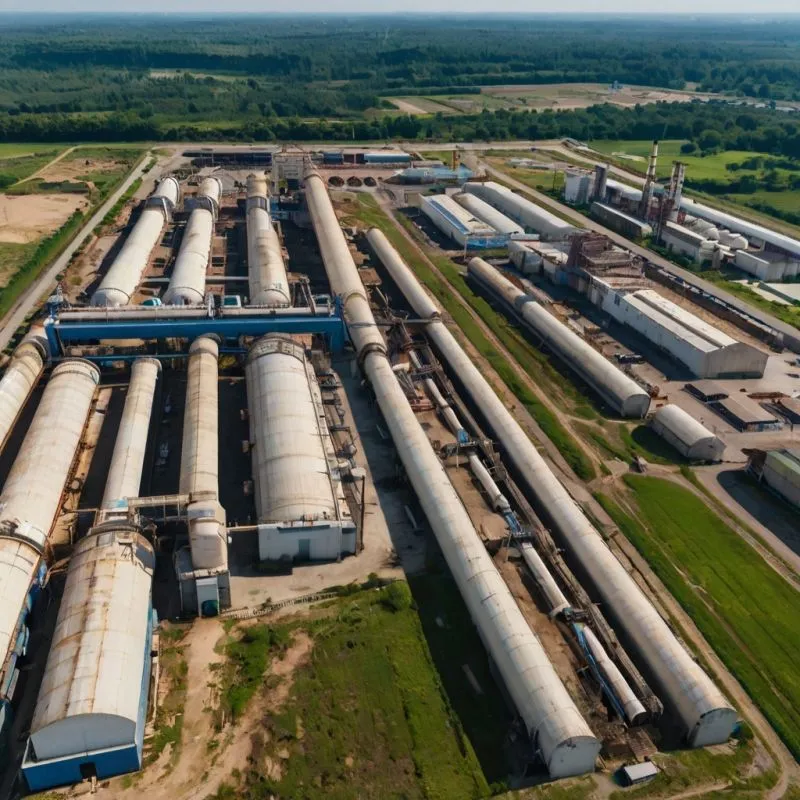
Relokacja linii produkcyjnych jest złożonym procesem, który wymaga starannego planowania i precyzyjnej realizacji na każdym etapie. Od demontażu maszyn, przez ich transport, aż po ponowne uruchomienie w nowej lokalizacji każda faza ma istotne znaczenie dla zapewnienia ciągłości produkcji oraz minimalizacji przestojów. Poniżej wyjaśnimy każdy z kroków relokacji linii produkcyjnych.
Na początku tego procesu konieczne jest dokładne zrozumienie struktury i funkcji każdej maszyny, co umożliwia bezpieczne i efektywne jej rozmontowanie. Specjalistyczne narzędzia i techniki są niezbędne, aby uniknąć uszkodzeń mechanicznych i zachować integralność sprzętu. Wszystkie elementy muszą być odpowiednio oznakowane i zapakowane, aby zapewnić łatwość montażu w nowej lokalizacji. Szczególną uwagę należy zwrócić na wrażliwe komponenty elektryczne i elektroniczne, które wymagają specjalnych warunków przechowywania i transportu.
Przestrzeganie norm bezpieczeństwa oraz dokładna dokumentacja każdego etapu demontażu są istotne, aby zminimalizować ryzyko i zapewnić płynne przejście do kolejnych faz relokacji. Dzięki skrupulatnej pracy specjalistów, demontaż urządzeń może przebiec sprawnie, minimalizując przestoje i przygotowując grunt pod skuteczne ponowne uruchomienie produkcji w nowej lokalizacji.
Pakowanie maszyn oraz transport do nowej lokalizacji
Każdy element maszyny musi być odpowiednio zabezpieczony przed uszkodzeniami mechanicznymi i wpływem czynników atmosferycznych. Specjalistyczne materiały pakujące, takie jak folia bąbelkowa, pianka ochronna, a także skrzynie transportowe, są niezbędne, aby zapewnić bezpieczeństwo delikatnym komponentom. Ponadto, każda część musi być dokładnie oznakowana, co ułatwi jej identyfikację i montaż w nowym miejscu. Ważnym aspektem jest również sporządzenie szczegółowej dokumentacji, która zawiera informacje na temat zawartości każdego opakowania, instrukcji dotyczących jego obsługi oraz szczególnych wymagań transportowych. Sprawdzone relokacje fabryk znajdziesz także na https://pserwis.pl/oferta/transfery-linii-produkcyjnych-i-urzadzen-przemyslowych
Profesjonalne firmy zajmujące się relokacją korzystają z zaawansowanych technologii, takich jak systemy śledzenia GPS, aby monitorować trasę transportu i zapewnić bezpieczeństwo ładunku. Transport maszyn często wymaga specjalistycznych pojazdów, takich jak naczepy niskopodwoziowe, które umożliwiają przewóz dużych i ciężkich urządzeń. Warto również uwzględnić aspekty logistyczne, takie jak uzyskanie odpowiednich zezwoleń oraz koordynacja z lokalnymi władzami, aby zapewnić płynny przebieg transportu.
Montaż linii produkcyjnej w nowym miejscu
Na początek, wszystkie elementy maszyn muszą być starannie rozpakowane i sprawdzone pod kątem ewentualnych uszkodzeń powstałych podczas transportu. Następnie, zgodnie z wcześniej przygotowanym planem, przeprowadza się montaż poszczególnych modułów, zaczynając od elementów bazowych i konstrukcyjnych, a kończąc na bardziej zaawansowanych komponentach mechanicznych i elektrycznych. Kluczowe jest przestrzeganie wszystkich norm bezpieczeństwa oraz specyfikacji technicznych, aby zapewnić prawidłowe działanie linii produkcyjnej.
Montaż wymaga współpracy zespołu ekspertów z różnych dziedzin, w tym inżynierów mechaników, elektryków oraz automatyków, aby zapewnić harmonijną integrację wszystkich systemów.
Uruchomienie oraz testy linii produkcyjnych
Uruchomienie oraz testy linii produkcyjnych to finalny etap procesu relokacji, istotny dla zapewnienia jej efektywnego funkcjonowania. Po zakończeniu montażu, linia produkcyjna musi zostać dokładnie przetestowana pod kątem wydajności i zgodności z określonymi standardami jakości. Proces ten obejmuje uruchomienie wszystkich systemów, kalibrację maszyn oraz wykonanie serii testów operacyjnych, które mają na celu wykrycie i eliminację ewentualnych usterek.
Przeprowadza się testy obciążeniowe oraz symulacje produkcyjne, aby upewnić się, że linia jest gotowa do pełnej eksploatacji. W trakcie testów monitorowane są kluczowe parametry operacyjne, takie jak tempo produkcji, jakość wytwarzanych produktów oraz zużycie energii. Na podstawie wyników testów dokonuje się niezbędnych korekt i optymalizacji, co pozwala na osiągnięcie maksymalnej efektywności.
Autor: Materiał partnera